
Putaway Process
The Putaway Process involves strategically placing received goods in the warehouse, optimizing storage, and preparing them for future operations:
Configuration and Area Selection
StoreTrack’s settings determine where items should be stored, based on criteria like shelf life, size, and demand.
Reserve vs. Prime Area
Goods are directed to either the prime area (high-demand, fast-moving items) or reserve area (overflow or low-demand products).
Dynamic Bin Mapping
The system automatically allocates bins in the reserve area based on available space and product specifications, maximizing space efficiency.
Storage in Reserve Area
Items are stored in the reserve area if they are not immediately needed in the prime area. The system ensures efficient utilization of storage space.
Accessibility and Retrieval
Items stored in the reserve area are still easy to retrieve when needed for restocking or order fulfillment.
Stock Visibility
StoreTrack ensures that both prime and reserve areas are constantly monitored, with up-to-date visibility into inventory levels.
Putaway Status Updates
Once goods are placed, their status is updated in the system to indicate they are ready for further processes.
Multi-location Storage
For larger warehouses, goods may be stored in multiple locations or zones within the same area. StoreTrack optimizes and manages these multiple locations for ease of access.
Integration with Refill Process
The Putaway process feeds directly into the Refill process, ensuring that stock is always available for order picking.
Back to Step 2
Go to Step 4
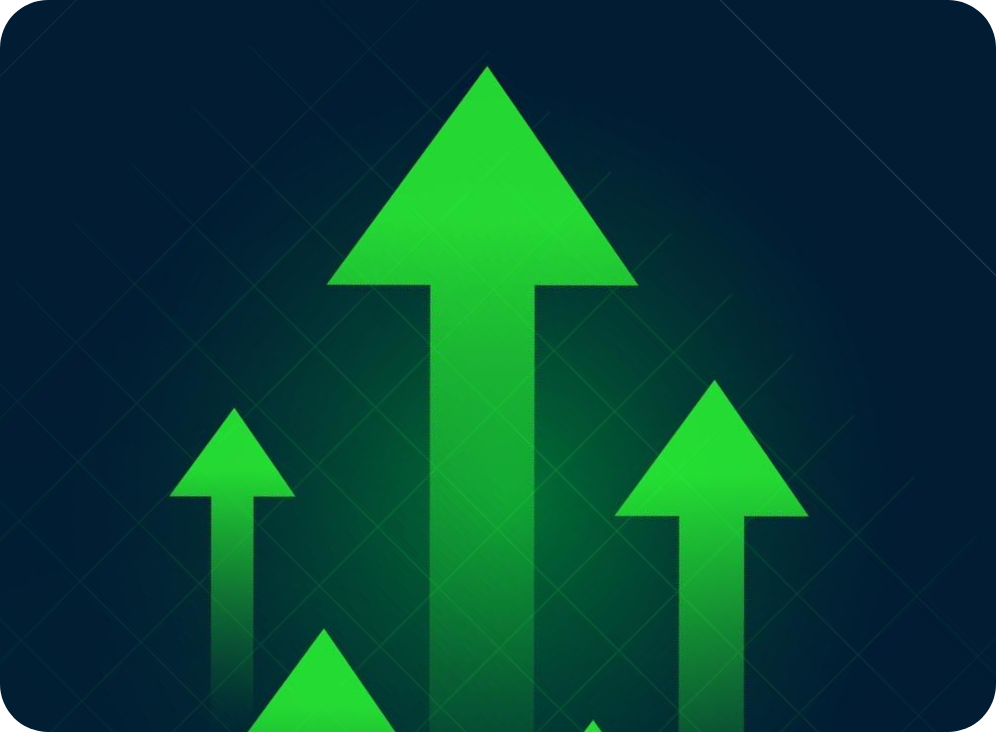
Experience the Power of Paperless Operations! Discover the future of godown management with StoreTrack.
Contact us today for a personalised demo and see how we can take your inventory control to the next level.