
Refill Process
The Refill Process in StoreTrack ensures that stock levels in the prime area are maintained, supporting uninterrupted order fulfillment and sales activities:
Stock Depletion and Refill Necessity
When stock levels in the prime area fall below a preset threshold, the system automatically triggers a refill request.
StoreTrack Document Generation
A “Godown to Godown Transfer” document is created to initiate the transfer of goods from the reserve area to the prime area.
Transfer Preparation
A team is assigned to prepare goods for movement from the reserve area to the prime area, ensuring a smooth transfer.
Picker’s Role
A picker is tasked with retrieving the required goods from the reserve area based on the details in the Transfer document.
Tout Assignment and Movement
The picked items are placed into a tout (temporary holding container) for easy movement between areas.
Prime Area Picker’s Action
Once the tout arrives in the prime area, the prime area picker scans the tout and places items in the designated bins.
Stock Availability for Further Processes
Once the items are replenished, they are now available for picking and processing, ensuring quick turnaround times for order fulfillment.
Seamless Sales and Distribution
The successful completion of the Refill process ensures that the warehouse is stocked with the right items for ongoing sales and distribution activities.
Performance Metrics
StoreTrack can generate performance reports for the refill process, helping to optimize the replenishment workflows and identify potential bottlenecks.
Automatic Stock Updates
As items are moved, the system automatically updates the inventory to reflect accurate stock levels across both reserve and prime areas.
Back to Step 3
Go to Step 5
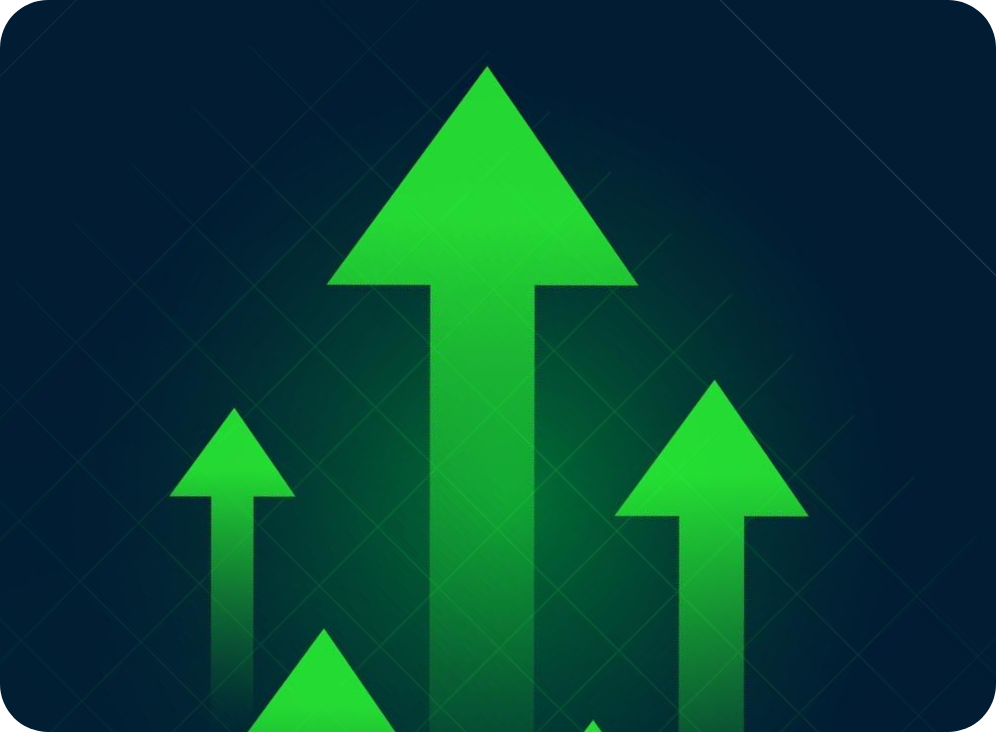
Experience the Power of Paperless Operations! Discover the future of godown management with StoreTrack.
Contact us today for a personalised demo and see how we can take your inventory control to the next level.